Choosing the right custom wiring harness is critical to the success of any complex system. A harness bundles many conductors into a single assembly, so its design directly affects electrical performance, reliability, cost, and delivery. This guide walks through seven key specifications to evaluate when sourcing a Custom Wiring Harness. We’ll explain why each spec matters, what to look for, and how it affects performance, cost or lead time. Wherever relevant, we’ll highlight how Infinite Harness can help – with low MOQ, rapid prototyping and expert support for sectors like Industrial & Robotics, Automotive & E-Mobility, and Medical & Healthcare.

Table of Contents
Toggle1. Conductor Gauge and Material (Current Capacity)
The wire gauge (thickness) and conductor material determine how much current the harness can safely carry. In North America, wire is sized by AWG: a smaller AWG number means a thicker wire with higher ampacity. Always start by calculating the maximum current draw of each circuit. Undersized wire can overheat or cause excessive voltage drop; in practice this can lead to intermittent faults or even fires. For example, an undersized wire in an automotive 12V circuit may cause lighting or powertrain malfunctions. Conversely, using a wire thicker than needed increases cost and bulk.
When specifying gauge, also account for harness bundling: tightly bound wires dissipate heat less efficiently, so each wire’s ampacity may need to be derated or a larger size chosen. Long harness runs (common in vehicles and machinery) incur voltage drop; a heavier gauge may be needed to keep voltage drop acceptable in a 12–48V system. Material matters too: copper (often tinned for corrosion resistance) is typical for high-current applications. Aluminum or copper-clad aluminum (CCA) may save weight/cost but have lower conductivity, so gauge must be adjusted.
What to look for: Specify the expected current (peak and continuous) per circuit and consult ampacity tables. Verify the supplier uses the correct AWG/metric size and copper grade. Ask about plating (tin vs bare) for solderability or corrosion resistance. Confirm the harness will be tested to handle the required current without overheating. This ensures reliable operation without excess weight or cost.

2. Connectors and Terminations
A wiring harness is only as reliable as its connectors and terminations. High-quality connectors ensure a stable electrical connection and simplify maintenance; poor connectors can become the weakest link. “No connector, no electricity” – even a robust harness fails if the connectors fail. Select connectors rated for the circuit’s current and environment (sealed automotive plugs, rugged M8/M12 industrial connectors, or delicate medical LEMO plugs, for example). Ensure compatibility of mating styles and pin counts.
Pay special attention to crimp and contact quality. Most harnesses use crimped terminals: a proper gas-tight crimp ensures low resistance and prevents moisture ingress. Incorrect crimping can lead to loose joints that corrode internally, causing shorts or opens. During review, ask if your supplier uses verified crimp tools and inspection (e.g. crimp pull-tests). Also consider strain relief and overmolding: robust mechanical fixation prevents wires from breaking out of the connector under vibration or bending.
What to look for: Verify that connectors match the application (current rating, locking features, IP rating for water/dust, etc.). Check if the terminals are plated or sealed to prevent corrosion. Ensure terminations are fully supported by strain-relief boots or custom overmold (see Tests & Inspections). For high-mating cycles (e.g. consumer dock connectors), choose gold-plated or spring-contact pins. Finally, insist that the harness be tested (continuity and withstanding force) after assembly – as one company notes, UL certification requires traceability of every wire and connector for quality assurance.

3. Insulation and Jacket Material
The choice of wire insulation (and any overall jacket) impacts flexibility, chemical resistance, and temperature range – and can make a big difference in cost. Common materials include PVC (polyvinyl chloride), silicone, TPE, fluoropolymers (e.g. PTFE), and LSZH (low-smoke, zero-halogen) compounds. For general-purpose harnesses, PVC is popular because it is durable, UV-resistant and inexpensive. Its typical service temperature goes up to about 90–105°C. PVC’s low cost and wide availability make it a good choice for many factory and indoor applications.
In higher-stress applications, more advanced insulation may be needed. Silicone-insulated wire, for instance, supports a huge temperature range (as low as –80°C and up to +180°C) and offers exceptional flexibility and chemical resistance. This makes silicone wire ideal for automotive engines or aerospace where heat and vibration are extreme. Its downside is that silicone is softer and less abrasion-resistant than PVC. As Galaxy Wire explains, silicone is “extremely flexible” and highly UV and chemical resistant, but relatively “soft” (less durable) as a jacket.
Other materials serve niche needs: cross-linked polyolefin (XLPO/XLPE) offers higher heat resistance than PVC; PTFE (Teflon) covers up to ~200°C and is very chemically inert (used in aerospace and medical). LSZH jackets should be specified if toxic smoke must be minimized (see spec #5).
What to look for: Confirm that the insulation is rated for your environment. For hot engine bays or outdoors, use high-temp or UV-rated insulation. For chemical or oil exposure, choose resistant materials (PVC or fluoropolymer). For medical or clean-room equipment, ensure biocompatible or cleanable jacketing (e.g. medical-grade silicone or TPU). Remember that specialty insulations cost more, so balance need vs budget. Ask about additional coatings (heat-shrink, braided sleeving) that may be applied to specific segments for extra abrasion protection or identification.

4. Shielding and EMI Protection
In data, sensor or signal harnesses, electromagnetic interference (EMI) can corrupt signals, so shielding is often critical. A shielded harness includes metal foil or braided shielding around one or more conductor bundles to block external noise. The shield works by (1) reflecting incident EMI away from the conductors, and (2) providing a path to ground so noise is drained around the wires. Without a shield, noisy motors or radio equipment nearby could induce unwanted currents into your cable.
There are two common shield types: foil shield (a thin aluminum laminate wrapped fully around the conductor bundle) and braid shield (a woven mesh of tinned copper or aluminum strands). Foil shields provide 100% coverage and are great for high-frequency noise, but they offer less durability. Braided shields (70–90% coverage typical) are heavier and more rugged, and they excel at attenuating low-frequency EMI. For best protection, designs may use both (foil + braid). In high-flex or tight spaces, spiral (woven in a helix) shields are sometimes used.
What to look for: If your application involves long wire runs, motors, or RF equipment, specify a shielded harness. Decide if you need 360° foil coverage, a braid, or both – note that braids add cost and weight. For automotive/E-Mobility or high-speed data (e.g. CAN/LIN, camera feeds), shielding is often required. Also consider connector shielding (metal backshells or overmolds) to maintain ground continuity. Finally, ensure any exposed shield ends are properly terminated (grounded) at the connectors or chassis. A well-shielded harness can dramatically improve signal integrity and prevent intermittent faults.
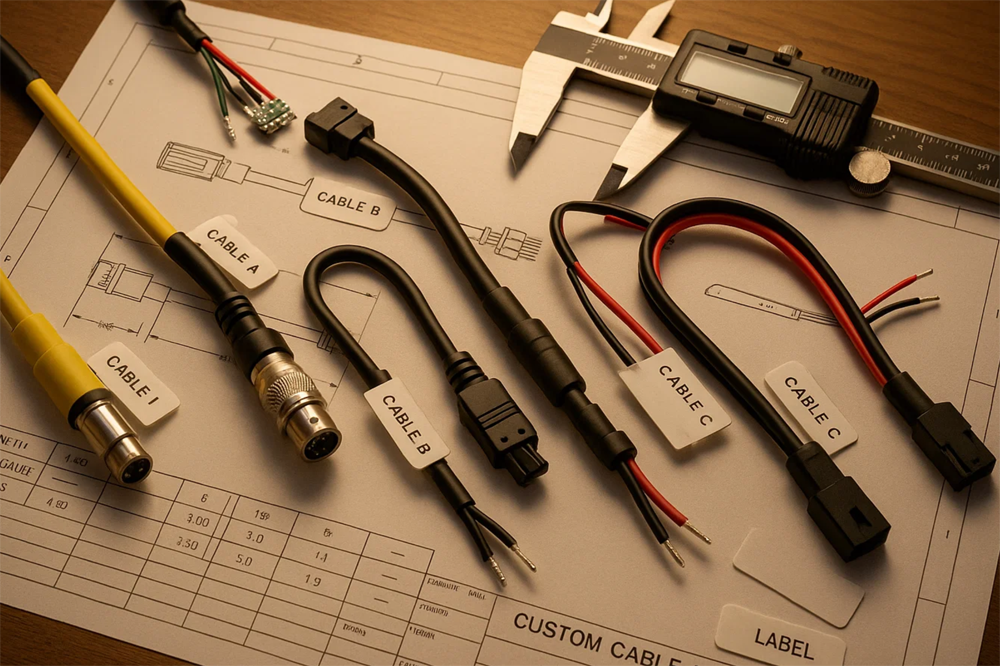
5. Environmental Ratings & Compliance
A wiring harness must survive its operational environment. This includes temperature extremes, moisture, chemicals, dust, vibrations, and even fire safety. For instance, outdoor or marine applications may require connectors and cables rated at IP67 or above (waterproof up to 1m). Ingress Protection (IP) ratings tell you exactly how a connector or enclosure is sealed (e.g. IP67 = dust-tight and water immersion resistant). In very humid or corrosive environments, specifying tinned copper conductors or corrosion-resistant metals can also improve lifespan.
Temperature is another critical factor. Standard PVC is fine up to ~80–105°C, but under-the-hood automotive or inside engines may spike higher. There, silicone or cross-linked materials with higher heat ratings are needed. For low-temperature use (e.g. freezer/freezer equipment), check the insulation’s minimum temp rating.
Fire and safety ratings must also be considered. Many industries require cables with flame-retardant jacketing (e.g. UL VW-1 or UL94 V-0 ratings). In public buildings, transportation or medical facilities, Low-Smoke Zero-Halogen (LSZH) materials are often mandated. LSZH cables emit minimal toxic smoke and no corrosive halogen gas if burne. As Galaxy notes, LSZH cable is “specified for use in highly populated, enclosed public spaces where flame resistance, low smoke production and reduced toxic/corrosive gas emissions are critical”.
Finally, ensure all components meet industry certifications. The supplier should comply with relevant standards: for electronics wiring, IPC/WHMA-A-620 (assembly acceptance) and IPC-A-610 are common benchmarks. UL or CSA listings on the wire or connectors indicate testing to safety standards. Seek ISO 9001 (or IATF 16949 for automotive) certified manufacturers. As one industry leader states, they inspect every harness to IPC/WHMA-A-620D and hold UL & ISO 9001:2015 certifications.
What to look for: Specify the needed IP rating for moisture and dust. Define operating temperature range and any chemical exposures. Ask if the harness uses flame-retardant or LSZH insulation if required. Verify the supplier’s certifications (UL/CSA, IPC/WHMA-A-620, ISO 9001). Check for special requirements like RoHS/REACH compliance on materials. These factors affect reliability: the wrong environment rating can cause premature failure, whereas higher ratings often raise cost.

6. Harness Configuration & Complexity
The physical layout and complexity of the harness is a key spec for performance, ease of installation, and cost. This includes the number of circuits (wire count), branch points, cable lengths, and any custom shaping or bundling. A harness with many branches and connectors requires more labor to assemble and test. Conversely, a simple straight-through cable is quicker and cheaper. Procurement managers should look at the harness drawing or sample to ensure it matches the application’s geometry.
For space-constrained systems (like those in Industrial & Robotics or Automotive consoles), a slim, well-organized harness is vital. Infinite’s engineering team notes that in dense control panels or robotic arms, “We design slim-profile, flexible harnesses with labeled terminations for faster and safer installations”. Labeling or color-coding each branch can greatly simplify future maintenance. Also consider whether the harness needs to be formed (e.g. pre-bent) or if a straight bundle will do. Service loops or slack may be needed if equipment moves.
Assembly details also matter. Decide if the harness should be tied with tape, laced with string, or fixed with cable ties at certain points. Ask about strain-relief boots or overmolding at junctions. If the harness will be overmolded into a connector or assembly, ensure the mold geometry is included in the spec. Even small details like heat-shrink sleeves, splitter boot (for Y-junctions), or braided sleeving can add cost but improve durability and neatness. For instance, Galaxy Wire mentions that harnesses may include custom colors, heat-shrink coatings, and labeling for identification.
What to look for: Provide a full harness drawing or 3D model to the supplier. Confirm the exact wire lengths, breakouts and connectors match the equipment. Check for specified bend radii and any weight/volume constraints. Request wire labeling or color-coding if helpful. For complex multi-branch harnesses, verify that the supplier can pre-configure and test each branch separately. Well-planned configuration reduces errors and installation time, but note that each branch and unique termination adds assembly time and cost.

7. Production Flexibility, Lead Time & MOQ
Finally, consider the sourcing logistics: the supplier’s minimum order, prototyping speed, and responsiveness. For many projects (especially in R&D or medical devices), only a few prototypes or small batches are needed – high MOQs can be a showstopper. Infinite’s site emphasizes that we don’t set a minimum order quantity (MOQ) and specialize in “small to medium-volume production”. This means even one-off prototypes or runs of 10–100 units are welcome, unlike larger contract manufacturers.
Also check lead times and prototyping capability. Fast iteration can drastically speed up development. Infinite’s Quick Turn Available service offers rapid prototypes in as little as 3–5 business days and low-volume runs (10–500 sets) in 5–10 days. (Even standard custom harnesses can be quoted within 24 hours.) Having a quick-turn partner means you can validate your design before committing to large production.
When comparing suppliers, ask how quickly they can quote and deliver samples. Some suppliers automate quoting and production; Infinite’s automated work instructions and high-speed processing equipment keep “lead times as short as 2–3 weeks” for many custom harnesses. Also inquire about engineering support – a good supplier will review your design for manufacturability and suggest cost-saving changes. For example, Infinite offers design feedback during quoting and will propose optimizations to reduce overall harness cost.
What to look for: Ensure your supplier can handle low-volume orders cost-effectively. Verify that their quoted lead time meets your schedule (and that they actually have in-house tooling, not rely on third-party molders). Ask if they offer expedited prototypes or quick-turn services. Check that they promise to quote your harness quickly (e.g. within a day or two). These factors don’t affect the electrical performance directly, but they can make or break a project by affecting time-to-market and inventory cost. A responsive manufacturer with no MOQ and short lead times can greatly accelerate project success.
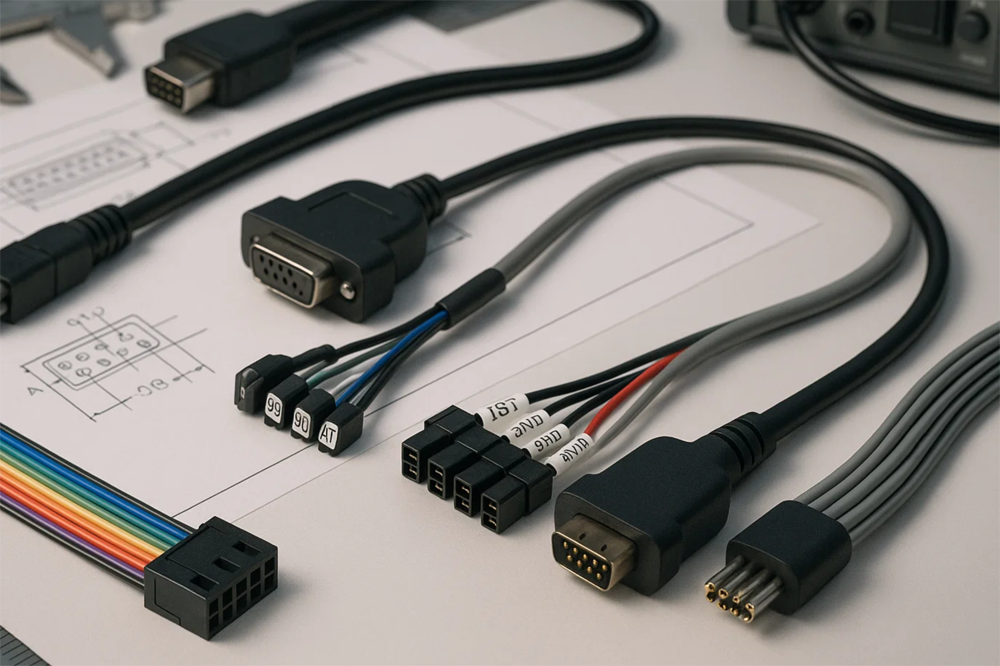
Conclusion
A well-sourced wiring harness strikes the right balance of electrical performance, durability, and cost. By carefully specifying conductor size, insulation, shielding, connectors, environmental ratings and assembly details, a procurement engineer ensures the harness won’t be the weak link in their system. At the same time, choosing a supplier that specializes in Custom Wiring Harness solutions for Automotive & E-Mobility, Industrial & Robotics and Medical & Healthcare markets can greatly simplify production. For instance, Infinite Harness offers low or no MOQs, fast prototyping, and full compliance with IPC, ISO, UL and RoHS standards. We invite you to explore our capabilities – from Electric Wire Harnesses for power distribution to Control Wire Harnesses for automation panels – and request a quote. Let our expertise in quick-turn custom harness manufacturing help keep your project on time and on spec.